【保存版】メッキの種類と加工方法の全貌をまとめました
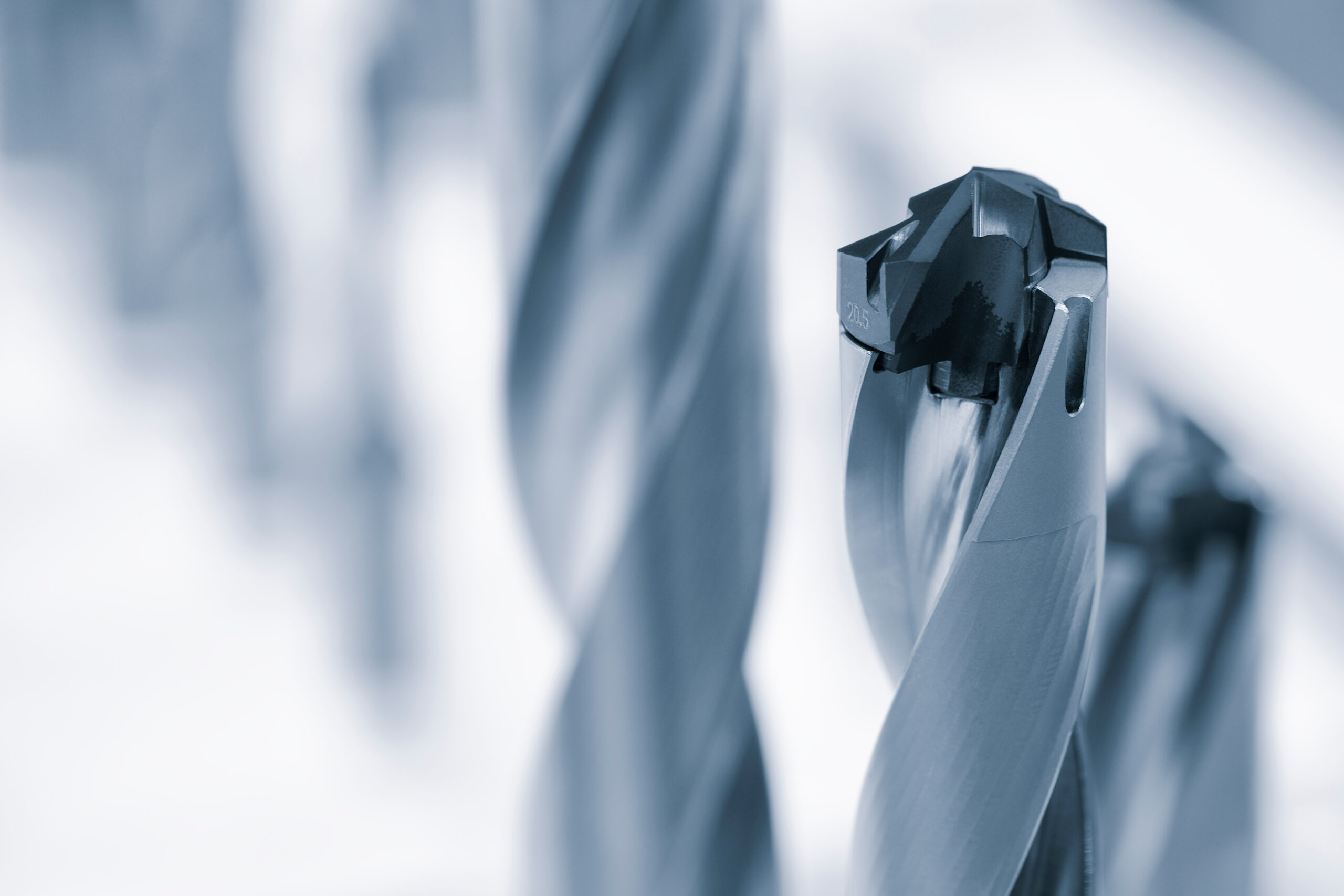
「メッキについて知りたいけれど、どこから手をつければいいのかわからない……」そんな悩みを抱えている方へ、この「メッキ保存版ガイド」をお届けします。
このガイドは、以下のような方々に最適です。
- メッキがどのようなものなのかを理解したい。
- メッキの種類や加工方法について詳しく知りたい。
- メッキを利用して自分のプロジェクトを成功させたいが、何を始めればいいか分からない。
- メッキの基本から最新の技術まで、全てを一度に学びたい。
メッキは、製品の耐久性や美観を向上させるために欠かせない技術ですが、多くの方がその詳細を理解せずにいます。正しいメッキの知識を持つことは、製品開発や製造において大きな差を生むことができます。
この記事では、メッキの基本的な概念から、さまざまな種類、加工方法、さらには実際の応用例までを網羅し、あなたの理解を深めるお手伝いをします。メッキの世界を一緒に探求していきましょう!
1. メッキ 種類 加工方法の基本知識
1-1. メッキとは何か
メッキとは、金属やプラスチックなどの表面に、他の金属を薄くコーティングする加工技術のことを指します。主に、耐食性の向上、美観の向上、電気伝導性や耐摩耗性の付与などを目的として行われます。産業分野では、装飾品、自動車部品、電子機器など幅広い用途で使用されています。
1-2. メッキ加工の歴史
メッキの起源は古代に遡り、紀元前のエジプト文明では金メッキが行われていた記録があります。近代においては、19世紀初頭に電気メッキ技術が発明され、産業革命とともに急速に発展しました。現在では、精密加工技術とともに進化し、ナノレベルでのコーティングも可能になっています。
2. メッキ 種類 加工方法の種類と特徴
2-1. 電気メッキの特徴
電気メッキは、電解液中で被処理物を陰極とし、陽極から金属イオンを析出させて表面に金属膜を形成する方法です。
- 特徴:
- 薄く均一な膜厚が可能
- 処理時間や電流密度によって膜の性質を調整可能
- 装飾性と機能性の両立が可能
- 代表的な金属:
- ニッケル、クロム、金、銀、銅など
2-2. 無電解メッキの特徴
無電解メッキは、電気を使用せず化学反応により金属イオンを還元し、被処理物に金属を析出させる方法です。
- 特徴:
- 複雑形状や非導電体にも均一にメッキが可能
- 電源設備が不要
- 化学浴の管理が重要
- 代表的な用途:
- 電子基板(プリント基板)、自動車部品、プラスチックへの金属化
2-3. その他のメッキ方法
- 蒸着メッキ(真空蒸着):真空中で金属を加熱・蒸発させ、被処理物に付着させる方法。光学機器や装飾品で用いられる。
- スパッタリング:プラズマを用いて金属原子を飛ばし、表面に堆積させる方法。薄膜形成に優れる。
- 溶融メッキ(溶融亜鉛メッキなど):金属を溶かした浴に素材を浸すことで被膜を形成。耐候性が高く建材などに使用。
3. メッキ 種類 加工方法の目的とメリット・デメリット
3-1. メッキ加工の目的
メッキは以下のような目的で行われます。
- 耐食性の向上:錆びや腐食から素材を保護
- 装飾性の向上:見た目を美しくする(例:金メッキ)
- 導電性の付加:電気部品などでの導通性向上
- 耐摩耗性の強化:摩擦による劣化を防ぐ
3-2. メッキのメリット
- 加工コストが比較的低い(特に量産時)
- 複雑な形状でも対応可能
- 様々な機能性を後付けできる
- 表面仕上げの均一性が高い
3-3. メッキのデメリット
- 下地処理や浴液管理が不適切だと品質が低下
- 厚膜化には不向き(特に電気メッキ)
- 使用する金属によっては環境負荷が高くなる
- 一部のメッキは剥がれやすく、耐久性に課題あり
メッキ技術は用途や求められる機能に応じて多様な方法が存在し、選定によって製品の品質やコストに大きく影響します。
4. メッキ 種類 加工方法の工程と具体的な方法
4-1. メッキ加工の基本工程
メッキ加工は金属表面に薄い金属膜を形成するプロセスで、以下のような基本的な工程に沿って行われます。
- 脱脂
油分や有機汚れを除去。アルカリ洗浄や溶剤洗浄が主流。 - 水洗
脱脂剤や洗浄成分を洗い流す。 - 酸洗い(スケール除去)
金属表面の酸化皮膜やスケール(酸化物)を取り除く。希硫酸・塩酸などを使用。 - 活性化処理
表面をメッキしやすい状態にするため、酸による表面活性化などを行う。 - メッキ処理(主工程)
電気メッキ、無電解メッキなど、選定されたメッキ方式で金属膜を形成。 - 水洗(再)
メッキ液を十分に洗い流す。残留液が腐食や変色の原因になる。 - 乾燥・仕上げ処理
エアブローや加熱乾燥により水分除去。必要に応じて研磨やパッシベーション(防錆処理)を実施。
4-2. 各メッキ方法の詳細な工程
電気メッキの工程
- 電解液の調整(メッキ浴の設定)
- 被処理物の陰極設置と電流制御
- メッキ厚の調整(時間と電流密度によって管理)
- 仕上げ・乾燥
※ニッケルメッキやクロムメッキでは、光沢・無光沢の調整もこの工程で行われます。
無電解メッキの工程
- 化学浴の準備(温度・pH管理が重要)
- 被処理物の浸漬
- 自己還元反応により金属が析出
- 所定時間で引き上げ
- 乾燥・研磨処理
※均一な被膜形成が可能なため、複雑形状やプラスチックにも対応。
溶融メッキ(例:溶融亜鉛メッキ)
- 素材の前処理(脱脂・酸洗い)
- フラックス処理(酸化防止)
- 溶融亜鉛槽に浸漬(450℃前後)
- 引き上げ・冷却・仕上げ処理
※耐候性が高く、構造物や建築部材などに使用される。
5. メッキ 種類 加工方法を発注する際の注意点
5-1. 発注前の準備
発注をスムーズに行うために、以下の情報を明確にしておく必要があります。
- 対象素材の種類と形状(例:鉄、アルミ、プラスチック)
- 希望するメッキ種別(例:ニッケルメッキ、無電解ニッケル、亜鉛メッキなど)
- 必要な機能性(例:防錆、装飾、導電性)
- 寸法・公差の有無(特に精密部品では重要)
- ロット数量・納期の希望
図面や用途説明を添付すると、業者との認識齟齬を防ぐことができます。
5-2. 信頼できる業者の選び方
発注先を選定する際は以下の点をチェックしましょう。
- 技術力と実績の確認:過去の加工事例や取引先実績をチェック
- 品質管理体制:ISO取得、RoHS対応など品質基準の有無
- 対応力と納期管理:短納期対応やカスタム対応の可否
- 見積もりの明確性:単価、加工日数、送料などの内訳明記
- アフターサポート:不良時の対応や再加工の可否など
実際の加工サンプルを見せてもらったり、工場見学が可能であれば、より確かな判断が可能です。
メッキ加工の成功は「目的に合った種類と方法の選定」と「信頼できる業者との連携」にかかっています。明確な仕様提示と双方向のコミュニケーションが品質確保の鍵となります。
まとめ
この記事では、メッキの種類や加工方法について詳しく解説しています。電気メッキ、無電解メッキ、金属メッキなどの各種メッキ技術の特徴や用途、さらにはその工程やメリット・デメリットを網羅。メッキの選び方や最新の技術動向も紹介しており、業界関係者や興味を持つ方にとって必見の内容です。