設計段階でのコストダウン手法:金属加工図面の最適化ガイド
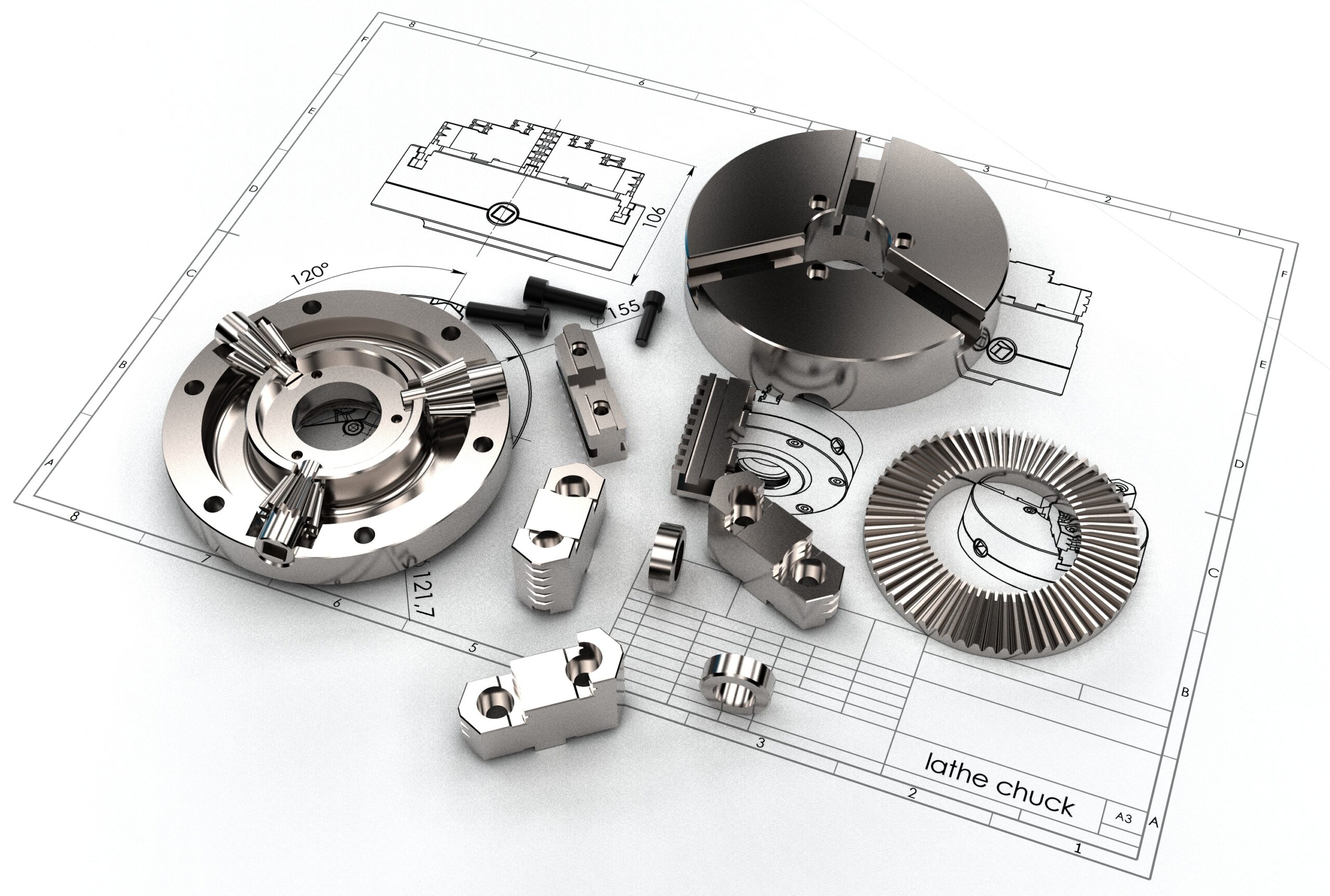
製品の設計を行う際、コストの削減は常に重要なテーマです。「設計の段階でコストダウンを図りたいが、何をどうすれば良いのか分からない…」そんな悩みを抱える方は少なくありません。そこで、このガイドでは、金属加工に関わる図面を最適化することで、効果的なコストダウンを実現する方法をご紹介します。
この記事は、以下のような方に最適です。
- 金属加工業界で働いているが、設計段階のコスト管理に悩んでいる方。
- 効率的な設計手法を学び、コストを削減したい方。
- 金属加工の図面を見直し、無駄を省きたいと考えている方。
設計の質とコストのバランスを取ることは、競争力を維持するために欠かせません。この記事を通じて、金属加工図面の最適化がどのようにコストダウンに寄与するのか、具体的な手法やポイントを理解し、実践できる知識を得ていただければ幸いです。さあ、一緒に効率的な設計を目指しましょう!
1. 設計 コストダウン 金属加工 図面の重要性
製造現場におけるコストダウンの鍵は、設計段階でいかに無駄を削減し、効率化を図るかにあります。特に金属加工の分野では、図面の内容が品質とコストに直結するため、設計者の意図を正確に伝える図面作成が極めて重要です。
1-1. 設計とコストダウンの関係
- 設計段階での判断が、材料費・加工費・納期に大きく影響します。
- 無理のない加工形状や、公差の適正化は、コストを大幅に左右します。
- 製造側と早期にすり合わせを行うことで、試作回数や手戻りを削減可能です。
1-2. 金属加工における図面の役割
- 加工現場にとって、図面は「作業指示書」であり、情報伝達の中心です。
- 設計者の意図が曖昧な図面は、加工ミスや手戻り、追加工の原因になります。
- 寸法、加工指示、仕上げ条件、公差などの明記が不可欠です。
2. 図面作成における具体的なコツ
2-1. 図面の基本要素
要素 | 説明 |
---|---|
寸法線 | 必要な寸法を明確に記載。加工基準が伝わるように統一。 |
公差 | 必要最小限の公差に限定し、加工コストの抑制に貢献。 |
材質 | 材料の明示により、加工性やコストに影響する部分を明確化。 |
表面仕上げ | 指示があることで、不要な追加工を防止できる。 |
加工指示 | 穴あけ、溶接、面取りなど、具体的な加工内容の記載。 |
2-2. 注意すべきポイント
- 過剰な精度要求はコスト増の原因に。
- 加工方向を無視した設計は追加工程を招く。
- 部品の組立順を考慮した設計と指示が必要。
2-3. 効率的な図面作成のためのツール
ツール名 | 特徴 |
---|---|
AutoCAD | 2D図面作成に強く、機械加工における基本ソフト。 |
SolidWorks | 3D CADとして人気。形状確認や干渉チェックに便利。 |
Fusion 360 | クラウドベースで共同作業に強み、軽量で学習コストも低い。 |
Jw_cad | 無償で利用可能な日本発のCAD。簡易的な図面作成に便利。 |
3. コストダウンを実現するための設計ポイント
3-1. 材料選定の重要性
- 材料の特性を理解し、加工性・入手性・単価を総合的に考慮。
- 高価な材料よりも、汎用品や既製材で代替できないか検討することが有効。
- 材料ロス(端材)の発生を抑える形状や寸法設計もポイント。
3-2. 製造プロセスの最適化
- 最小工程で製作できる形状に設計。
- 標準的な加工方法(フライス・旋盤など)で対応可能か確認。
- 二次加工や溶接工程の削減もコストに直結。
3-3. 設計変更によるコスト削減
- 機能に影響を与えない変更であれば、積極的に再設計を検討。
- 試作品や初期ロットから得たフィードバックを設計に反映。
- 加工工場からの意見をもとに形状や公差を見直す。
4. 設計の意図を図面に反映させる方法
製品設計において「意図を図面に落とし込む力」は、加工品質とコスト、納期に直結する重要なスキルです。現場とのすれ違いを防ぎ、確実にモノづくりを進めるためには、単に正確な寸法を描くだけでなく、図面を通じて“伝える”意識が求められます。
4-1. コミュニケーションの重要性
- 加工現場とのすり合わせが不十分な場合、設計意図と実際の加工内容にズレが生じ、品質トラブルや再加工の原因となります。
- 特に板金や切削、溶接などの各加工工程では、「どの順番で加工されるのか」「どこにストレスがかかるのか」といった製造側の視点を取り入れることが不可欠です。
- 設計初期段階から現場エンジニアや製造パートナーとの意見交換を行い、加工の可否・コスト・リードタイムといった観点で“作りやすい設計”を意識しましょう。
4-2. 図面における注釈の活用
- 寸法や公差だけでなく、設計者の意図を注釈に明記することが重要です。例えば、「この面は外観重視」「この穴は後加工で仕上げ」など、見た目では伝わらない情報を補足します。
- 板金でよくあるのが「曲げ方向」や「仕上げ表面指定」などの記載不足による誤加工。こうした情報は文字や矢印、断面スケッチなどで具体的に示しましょう。
- また、特記事項欄や備考欄を活用して「現場に考慮してほしい点」「代替案があれば相談可能」といった柔軟な意図も伝えることで、意思疎通のロスを防げます。
4-3. フィードバックの取り入れ方
- 初回試作や少量ロットで得られた現場からの意見は、次回設計に必ず活かすべき貴重な情報源です。
- 「溶接が難しい位置にある」「冶具の干渉があった」「公差の管理が厳しすぎる」などのフィードバックを積極的に収集し、図面に反映することで設計の品質が着実に向上します。
- また、フィードバックを得るための仕組み(例:加工後に現場レビューシートを記入)をあらかじめ整えておくと、スムーズな改善が可能になります。
5. 機械加工に関する基礎知識
金属加工における「機械加工」は、製品の寸法精度・仕上げ品質・量産効率において決定的な役割を持ちます。加工方法の選定や機械の性能、加工条件の設定次第で、コストや製品の完成度が大きく変わります。
5-1. 金属加工の種類
- 旋盤加工:丸材の外径や内径の切削に用いられ、シャフト類や軸物の加工に特化。主軸に対して回転しながら切削工具を当てる方式。
- フライス加工(マシニング):平面や溝、穴、複雑な3D形状まで幅広く対応。加工面の自由度が高く、治具と組み合わせて多面加工も可能。
- ボール盤加工:穴あけ専用の工作機械。多品種小ロットに向いており、構造がシンプルなため扱いやすい。
- 放電加工(EDM):電気的に金属を溶かして削る加工法。硬い材料や微細形状、薄物の加工に向いており、金型製作などに多用されます。
- ワイヤーカット加工:電極線を用いた極めて精密な切断が可能。形状精度・角出しが必要な場合に活躍。
- レーザー・ウォータージェット加工:非接触で材料を切断。熱影響が少なく、樹脂や複合材など熱に弱い素材でも加工できます。
5-2. 加工精度とその影響
- 加工精度は製品の性能・信頼性に直結し、例えばシャフトのすき間がわずかに広いだけで回転不良や振動の原因となることがあります。
- 一般的な精密加工では±0.01mm以下の管理が必要な場合もあり、図面に記載する公差設定が極めて重要です。
- ただし、過剰な精度指定は不要なコスト増を招くため、用途に応じた「適正公差」を設計段階で見極めることがポイントになります。
5-3. 機械加工の最新技術
- 5軸マシニングセンタ:1回の段取りで複雑な立体形状を多面から加工可能。加工時間の短縮、精度向上、冶具削減に貢献します。
- IoT・スマートファクトリー化:センサーによって加工条件や機械状態を常時モニタリングし、トラブル予兆や最適条件をAIが提案。予知保全や加工の安定化に活かされています。
- ロボットによる自動搬送・段取り:加工機への材料供給・取り出し・検査を自動化。夜間無人運転や省人化を実現。
- CAMソフトの進化:3Dデータから最適な加工パスを自動生成し、複雑形状でも短時間で段取り・加工指示が可能。設計から加工への移行スピードが加速しています。
これらの基礎知識と最新技術を設計段階で理解しておくことで、現実的かつ効率的な加工設計が可能になります。
まとめ
金属加工図面の最適化は、設計段階でのコストダウンに不可欠です。無駄な材料を削減し、加工工程を簡素化することで、製造コストを低減します。また、標準部品の活用や、加工時間の短縮を図ることで、効率的な生産が可能になります。設計の段階での工夫が、全体のコスト削減に繋がります。