金属加工の精度を向上させるために知っておきたい5つのポイント
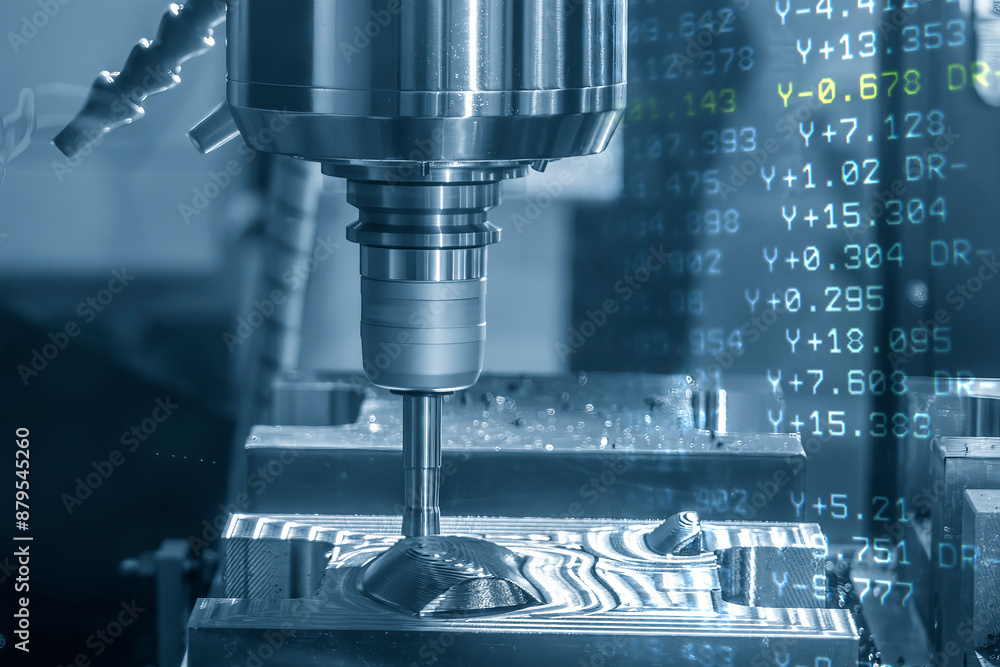
金属加工の分野において、精度は品質を左右する非常に重要な要素です。「金属加工の精度を上げるためのポイントは?」と疑問に思っている方も多いのではないでしょうか。特に製品の完成度や信頼性を求められる現代の製造業において、精密な加工は不可欠です。そこで、この記事では金属加工の精度を向上させるために知っておくべき5つのポイントを詳しく解説します。
もし「金属加工においてもっと高精度な製品を作りたい」と考えている方や、「どうすれば自社の加工精度を向上させられるのか?」と悩んでいる方がいれば、ぜひこのガイドを参考にしていただければと思います。これからのモノづくりに役立つ知識を一緒に深めていきましょう。精度を高めることで、製品の品質が向上し、顧客満足度も向上すること間違いありません。さあ、精密加工の世界へ一歩踏み出しましょう。
1. 金属加工の精度を上げるためのポイントは?
金属加工において、精度は非常に重要な要素です。高い精度を確保することは、製品の品質向上に繋がり、最終的な機能性にも大きく影響を与えます。精度を上げるためのポイントをいくつか紹介します。
1-1. 金属加工における精度向上の重要性
金属加工における精度向上は、製品の品質や機能を決定づける要因となります。特に、精密機械部品や自動車、航空機、医療機器など、高い性能が求められる部品では、精度が欠かせません。精度が低いと、以下のような問題が発生する可能性があります。
- 部品の不良や不具合
精度が不足していると、部品が所定の寸法や形状を満たさないため、組み立て時に不具合が生じたり、機能を果たさなかったりします。 - 品質の低下
精度が低いと、製品全体の品質が低下し、最終的な使用感や信頼性に影響を与えることがあります。 - コスト増加
精度の低い部品は再加工が必要になることが多く、その分コストが増加します。また、不良品が多い場合には、無駄な材料費や時間がかかり、最終的な生産コストが上昇します。
精度を向上させることは、製品の品質を確保し、無駄なコストや手間を削減するために不可欠です。次に、精度向上のための具体的なポイントを見ていきましょう。
2. 精度を左右する要因とは?
金属加工における精度は、さまざまな要因によって左右されます。これらの要因を適切に管理することで、高精度な部品の製作が可能になります。主な要因には以下のものがあります。
2-1. 加工機械の精度
加工に使用する機械の精度は、最終的な製品の精度に大きな影響を与えます。特にCNC(コンピュータ数値制御)マシンや高精度の工作機械を使用することで、微細な寸法を実現できます。これらの機械は、精密な動作と制御が可能であり、複雑な形状の加工にも対応できます。
- 機械のメンテナンス: 機械の状態が悪いと、加工精度が低下します。定期的なメンテナンスが不可欠です。
- 工作機械の設定: 加工条件や設定が適切でないと、精度が損なわれることがあります。
2-2. 使用する工具の状態
工具の摩耗や損傷が加工精度に影響を与えることがあります。特に切削工具が鈍くなると、加工時に振動が発生したり、切削力が不安定になったりして精度が低下します。
- 工具の選定: 適切な材料や形状の工具を選択することが精度向上に寄与します。
- 工具の摩耗管理: 工具が摩耗していないか、定期的にチェックすることが重要です。
2-3. 加工環境
加工を行う環境も精度に大きな影響を与えます。温度や湿度の変動、振動などが原因で、部品が収縮したり膨張したりすることがあり、これが精度の低下を招く可能性があります。
- 温度管理: 特に金属は熱膨張するため、一定の温度管理が必要です。
- クリーンな作業環境: 汚れやホコリが作業精度を損なう可能性があるため、作業場の清潔さを保つことが重要です。
2-4. 材料の特性
使用する金属材料の特性も精度に影響を与えます。異なる金属は硬さや熱膨張率が異なり、これが加工中に問題を引き起こすことがあります。
- 材料の均一性: 材料が均一でない場合、加工時に予測できない変形が生じる可能性があります。
- 適切な材料選定: 加工する部品に最適な材料を選ぶことが、精度向上に繋がります。
2-5. 加工者の技術力
最終的に、金属加工の精度は作業を行う技術者のスキルに大きく依存します。技術者が機械や工具の使い方、加工条件を適切に理解し、正確に操作することが求められます。
- 作業者の経験とスキル: 熟練した技術者は精度の高い加工を実現できますが、経験不足や技術的な問題が精度を損なうことがあります。
- 教育とトレーニング: 継続的な教育とトレーニングが精度向上に繋がります。
これらの要因を総合的に管理することが、金属加工における高精度な製品作りには不可欠です。精度向上には、機械、工具、環境、材料、技術者のスキルのすべてをバランスよく最適化する必要があります。
3. 切削加工の精度を上げるための具体的な方法
切削加工において高精度な部品を作るためには、さまざまな方法を組み合わせて精度向上に取り組むことが重要です。以下では、精度を向上させるための具体的な方法をいくつか紹介します。
3-1. 最適な切削条件の設定
切削加工の精度を向上させるためには、最適な切削条件を設定することが重要です。切削速度、送り速度、切り込み量などを適切に調整することで、加工精度が向上します。
- 切削速度の調整: 高すぎる切削速度では工具の摩耗が早まり、精度が低下する可能性があります。適切な切削速度を選定し、工具の耐久性を高めることが重要です。
- 送り速度の最適化: 送り速度が速すぎると、加工中に振動が発生し、精度に悪影響を与えることがあります。適切な送り速度を選定することが精度を保つためには不可欠です。
3-2. 高精度な工具選定
切削精度を確保するためには、使用する工具の選定が非常に重要です。工具の種類や材質、形状などが加工精度に大きく影響を与えるため、最適な工具を選定することが必要です。
- 工具のコーティング: コーティングされた工具は摩耗を抑え、長期間高精度な加工が可能になります。
- 工具の形状とサイズ: 加工する部品の形状に最適な工具を選ぶことで、精度が向上します。特に精密な加工には、高精度な工具が求められます。
3-3. ワークの固定と振動対策
加工中のワークの動きや振動を抑えることも、切削加工の精度を保つためには重要です。ワークがしっかりと固定されていない場合、加工中に微小な動きが生じ、精度が低下します。
- 適切な固定具の使用: ワークをしっかりと固定するために、クランプやチャックを適切に使用することが大切です。
- 振動の抑制: 加工中に発生する振動を抑えるために、機械のダンピング性能やワークの取り付け方を工夫します。特に高速加工を行う際は、振動の影響が精度に大きく影響します。
3-4. 温度管理
金属は温度変化によって膨張や収縮が起こるため、温度管理を徹底することが精度向上には不可欠です。特にCNC機械を使用する場合、周囲温度の変動が機械の精度に影響を与えることがあります。
- 冷却装置の使用: 切削中に工具やワークを冷却することで、温度上昇を防ぎ、精度を保ちます。
- 温度安定化環境の確保: 工場内の温度管理を徹底し、一定の温度条件下で加工を行うことが重要です。
3-5. 定期的な機械のメンテナンス
機械のメンテナンスを怠ると、精度が低下する原因となります。特に、機械のスライドやリニアガイドの磨耗、摩擦の増加などが精度に影響を与えることがあります。
- 定期的な校正: 加工機械の精度を定期的に確認し、必要に応じて校正を行うことが精度向上に繋がります。
- 機械の清掃と潤滑: 定期的な清掃と潤滑を行い、機械内部の摩擦や不具合を防ぎます。
3-6. 加工前の準備と検証
加工を始める前に、しっかりと準備を行い、検証することで精度を高めることができます。
- プログラムのチェック: CNC機械で加工を行う場合、プログラムが正確であるか事前にチェックすることが重要です。
- テスト加工の実施: 本加工を始める前に、テスト加工を行って精度を確認し、問題があれば調整を行います。
これらの方法を組み合わせて実践することで、切削加工の精度を向上させ、精密な部品の製作が可能になります。特に、加工条件、工具選定、機械のメンテナンス、ワークの固定方法を適切に管理することが、精度向上の鍵となります。
4. 高精度加工を実現するための基本的なポイント
高精度な加工を実現するためには、様々な要素が影響を与えます。これらをうまく組み合わせることで、加工精度を向上させ、要求に合った高精度な製品を作ることが可能となります。以下は、高精度加工を実現するための基本的なポイントです。
4-1. 機械の精度と安定性の確保
高精度加工を実現するためには、使用する機械の精度が非常に重要です。機械の精度が低ければ、高精度な加工はできません。また、加工中に機械の安定性が損なわれると、加工精度が低下します。
- 高精度なCNC機械の導入: 高精度なCNC機械を使用することで、微細な加工が可能となり、精度が向上します。特に、温度変化や振動に対する耐性を持つ機械が有利です。
- 機械の定期的な校正: 定期的な校正により、機械の精度を保つことができます。精度が狂ってしまうと加工結果に影響が出ます。
4-2. 適切な切削条件の設定
加工における切削条件(切削速度、送り速度、切り込み量)は、精度に直接的な影響を与えます。これらの条件が適切でない場合、工具の摩耗や部品の歪みが発生し、精度が低下します。
- 切削速度の最適化: 適切な切削速度を設定することで、工具の寿命を延ばし、精度を維持します。高すぎる切削速度では工具が早く摩耗し、低すぎる切削速度では加工時間が無駄になります。
- 送り速度と切り込み量の調整: 送り速度や切り込み量が不適切だと、加工精度が低下することがあります。最適な値を見極めて調整することが重要です。
4-3. 高精度な工具の選定
使用する工具は、加工精度に大きく影響します。工具の選定を誤ると、加工中に問題が発生し、精度が低下します。
- 工具の材質と形状の選定: 材質に適した工具を選ぶことで、加工中の摩耗を抑え、精度を保つことができます。精密な加工を行うためには、切れ味の鋭い工具を使用することが大切です。
- 工具のコーティング: 高精度加工には、耐摩耗性や熱伝導性の高いコーティングが施された工具を使用することが推奨されます。
4-4. ワークの固定方法の工夫
ワークがしっかりと固定されていないと、加工中に微細な動きが生じて精度が低下します。ワークの取り付け方法は、加工精度を高めるために重要な要素です。
- クランプの使用: ワークをしっかりとクランプすることで、加工中の微細な動きを防ぎ、精度が向上します。適切なクランプ方法を選択することが大切です。
- 治具の使用: 高精度な治具を使用することで、ワークの位置決め精度を高め、加工精度が向上します。
4-5. 温度管理と冷却の徹底
金属は温度の変化により膨張や収縮を起こすため、加工精度に影響を与えます。温度変化を抑えるためには冷却が不可欠です。
- 冷却液の使用: 切削中に冷却液を使用することで、工具やワークの温度上昇を抑え、加工精度を保つことができます。冷却液の種類や量を調整することがポイントです。
- 温度安定化環境の確保: 工場内の温度を安定させることで、金属の膨張を抑え、加工精度を維持できます。
4-6. 振動対策
加工中に発生する振動は、精度を大きく損なう原因となります。振動を抑えることが高精度加工には欠かせません。
- 振動吸収材の使用: 振動を吸収するための装置やマットを使用することで、加工中の振動を最小限に抑えることができます。
- 機械の設置場所の選定: 加工機械を設置する場所によっても振動が影響を受けることがあります。振動の少ない場所に機械を設置することが精度向上に繋がります。
4-7. 精度の監視とフィードバック
高精度な加工を実現するためには、加工中に精度を監視し、必要に応じて調整を行うことが重要です。
- オンラインモニタリングシステムの活用: 加工機械にセンサーを取り付けて、リアルタイムで精度を監視するシステムを導入することで、精度の維持が可能になります。
- 測定機器の使用: 加工後に精度を測定し、問題があれば即座にフィードバックを行うことで、精度を保つことができます。
これらの基本的なポイントを意識し、徹底的に管理することで、金属加工における高精度な部品を安定的に生産することが可能になります。
5. 穴加工における高精度仕上げの技術
穴加工は多くの金属加工で不可欠なプロセスであり、精度が要求される作業です。特に、高精度な穴加工を実現するためには、適切な加工技術と注意深い管理が必要です。以下に、穴加工における高精度仕上げの技術について説明します。
5-1. 高精度穴加工における基本技術
高精度な穴を開けるためには、加工機の設定や工具の選定が非常に重要です。適切な技術を駆使することで、寸法精度や表面品質を高めることができます。
- ドリル加工: 穴加工の中でも基本的な方法です。高精度な穴を開けるためには、ドリルの材質や刃先の形状を選ぶことが大切です。また、加工速度や送り速度も精度に影響を与えるため、最適な設定が必要です。
- リーマ加工: 穴の仕上げ加工で最もよく使われる方法です。リーマはドリル加工後に使用し、内径を精密に仕上げるために活用されます。リーマは高精度な仕上げが可能で、特に内径の寸法精度を高めることができます。
5-2. 穴加工の精度を高めるためのツール選定
ツールの選定は、高精度な穴加工の実現に直結します。工具の材質や形状によって加工結果が大きく異なるため、最適なツールを選ぶことが重要です。
- 高精度ドリルの使用: 高精度な穴を開けるためには、切れ味の鋭い高精度ドリルを選ぶことが必要です。高精度ドリルには、精密に研磨された刃先が施されており、精度の高い穴を開けることができます。
- コーティング工具の利用: コーティングされた工具を使用することで、摩耗や熱の影響を抑え、精度を維持することができます。特に高硬度の材料を加工する際には、耐摩耗性の高い工具を選ぶことが大切です。
5-3. 穴加工精度を高めるための加工条件
加工条件を適切に設定することで、穴加工の精度を高めることができます。加工条件には、切削速度、送り速度、切り込み量などが含まれます。
- 最適な切削速度の設定: 適切な切削速度を設定することで、工具の摩耗を抑え、精度を保つことができます。切削速度が高すぎると工具が早く摩耗し、低すぎると加工効率が悪くなります。
- 送り速度と切り込み量の調整: 送り速度や切り込み量も精度に大きく影響します。適切な値に調整することで、加工中の振動を抑え、精度が向上します。
5-4. 穴加工精度を保つための冷却と潤滑
加工中に発生する熱を抑えるために、冷却や潤滑は非常に重要です。冷却液や潤滑剤を適切に使用することで、加工精度を向上させることができます。
- 冷却液の使用: 切削中に冷却液を使用することで、温度上昇を抑え、工具の寿命を延ばすことができます。また、冷却液によって加工面が滑らかになり、精度が向上します。
- 潤滑剤の選定: 穴加工には潤滑剤も効果的です。適切な潤滑剤を選ぶことで、摩擦が減少し、加工中の熱の発生を抑えることができます。
5-5. 穴加工後の精度確認と調整
穴加工後には、仕上がりの精度を確認し、必要に応じて調整を行うことが重要です。精度確認を怠ると、後工程で問題が発生する可能性があります。
- 精密測定機器の使用: 加工後に精度を測定するための精密測定機器(マイクロメーターや投影機など)を使用することで、穴の寸法や形状が正確であることを確認できます。
- 後処理の調整: 精度が足りない場合、追加の仕上げ加工(リーマ加工やホーニングなど)を行うことがあります。これにより、寸法精度や表面品質をさらに向上させることができます。
5-6. 高精度穴加工のための振動管理
加工中の振動は、穴加工精度を大きく損なう原因となります。振動を抑えることは、精度向上に欠かせない要素です。
- 振動吸収技術の活用: 振動を抑えるための装置や技術を導入することで、加工精度を向上させることができます。特に、振動が精度に与える影響を最小限に抑えるための設計が重要です。
- 加工機の設置場所の最適化: 加工機を安定した場所に設置することで、加工中の振動を減少させることができます。
これらの技術を駆使することで、高精度な穴加工が可能となり、より高品質な製品の生産が実現します。
6. 自動旋盤を使用した金属加工の精度向上のポイント
自動旋盤は、金属加工の中でも高い精度を要求される作業に多く使用されています。効率よく高精度な加工を行うためには、適切な管理と技術が必要です。以下に、自動旋盤を使用した金属加工における精度向上のポイントを説明します。
6-1. 自動旋盤の基本構造とその精度管理
自動旋盤は、主に金属の切削や削り出し作業を行うための機械で、特に複雑な形状の加工に適しています。精度を向上させるためには、以下の基本構造と管理が重要です。
- 主軸と送り機構の精度: 自動旋盤の主軸は加工精度に大きく影響します。主軸の回転精度が悪いと、加工物の形状や寸法に誤差が生じるため、精度を確保するためには主軸のメンテナンスが欠かせません。また、送り機構の精度も重要で、送りの不正確さが寸法のズレを引き起こす原因となります。
- ツールホルダの調整: ツールホルダの取り付けが不正確だと、切削工具の位置がずれて加工精度が低下します。ツールホルダをしっかりと調整し、正確に設置することが求められます。
6-2. 高精度を実現するためのツール選定
適切なツールを選ぶことが、精度向上に大きく貢献します。自動旋盤で使用する切削工具の選定について、以下のポイントを押さえると良いでしょう。
- コーティングされた工具の使用: 高精度な加工を実現するためには、コーティングされた切削工具を使用することが有効です。コーティングにより摩耗が抑制され、より安定した加工が可能になります。また、加工対象となる素材に適したコーティングを選ぶことが大切です。
- 切削工具の材質: 高精度な加工をするためには、工具材質の選定も重要です。例えば、高硬度の金属を加工する場合、耐摩耗性や熱伝導性の高い材料(例:超硬工具)を選ぶことが求められます。
6-3. 加工条件の最適化
自動旋盤の精度向上には、加工条件を最適化することが欠かせません。加工条件には、切削速度、送り速度、切り込み量、クーラントの使用などが含まれます。
- 最適な切削速度と送り速度: 切削速度や送り速度を最適化することで、工具の摩耗を最小限に抑えつつ、精度を高めることができます。切削速度が速すぎると摩耗が早く進み、精度が低下しますが、遅すぎると加工時間が長くなり、効率が落ちます。送り速度も加工精度に大きく影響するため、最適な値を設定することが重要です。
- 切り込み量の調整: 一度に大きな切り込みを行うと、機械にかかる負荷が大きくなり、精度が損なわれる可能性があります。複数回に分けて切り込み量を少なくし、精度の高い仕上げを行うことが有効です。
6-4. クーラントと冷却の使用
加工中の冷却は、自動旋盤を使用した精度向上において非常に重要です。冷却液を適切に使用することで、以下のメリットがあります。
- 工具の温度管理: 切削中に発生する熱を抑えるために冷却液を使用することで、工具の温度が上がりすぎず、精度を保つことができます。高温になると、工具の摩耗が早く進行し、加工精度が低下する原因となります。
- 加工面の品質向上: 冷却液を使用することで、加工面の温度を均等に保ち、均質な表面品質を確保できます。これにより、完成した製品の寸法や表面状態が安定します。
6-5. 加工中の振動管理
自動旋盤での加工中、振動は精度に大きな影響を与えます。振動を最小限に抑えるための管理が精度向上には不可欠です。
- 振動吸収機構の導入: 加工機のフレームや基盤に振動吸収機構を導入することで、加工中の微細な振動を抑制できます。これにより、精度が向上し、仕上がりがより安定します。
- 切削条件の最適化: 振動が発生する原因の一つは、切削条件の不適切さです。最適な切削条件を選定することで、振動を減らし、精度を向上させることができます。
6-6. 加工後の品質チェックと調整
自動旋盤での加工が終わった後には、製品の精度を確認するための品質チェックが欠かせません。これにより、誤差を最小限に抑えることができます。
- 精密測定機器の使用: 加工後に精度を測定するために、マイクロメーターや三次元測定器を使用して寸法や形状を正確に測定します。これにより、問題が発生した場合は早期に発見し、修正することができます。
- 再調整や再加工: 測定結果に基づいて再調整が必要な場合、ツールの位置や切削条件を再設定し、精度を保つようにします。
自動旋盤を使用した金属加工の精度向上は、これらのポイントを確実に押さえることで実現できます。高度な技術と精密な管理が、安定した高精度な製品の生産に繋がります。
まとめ
金属加工の精度向上には、以下の5つのポイントが重要です。まず、適切な工具の選定とメンテナンスを行い、次に加工条件を最適化します。さらに、機械の校正を定期的に実施し、加工環境を整えることも大切です。データ分析を活用してプロセスを改善し、品質管理を徹底することで、精度が向上します。