クランクシャフトの切削工程完全ガイド
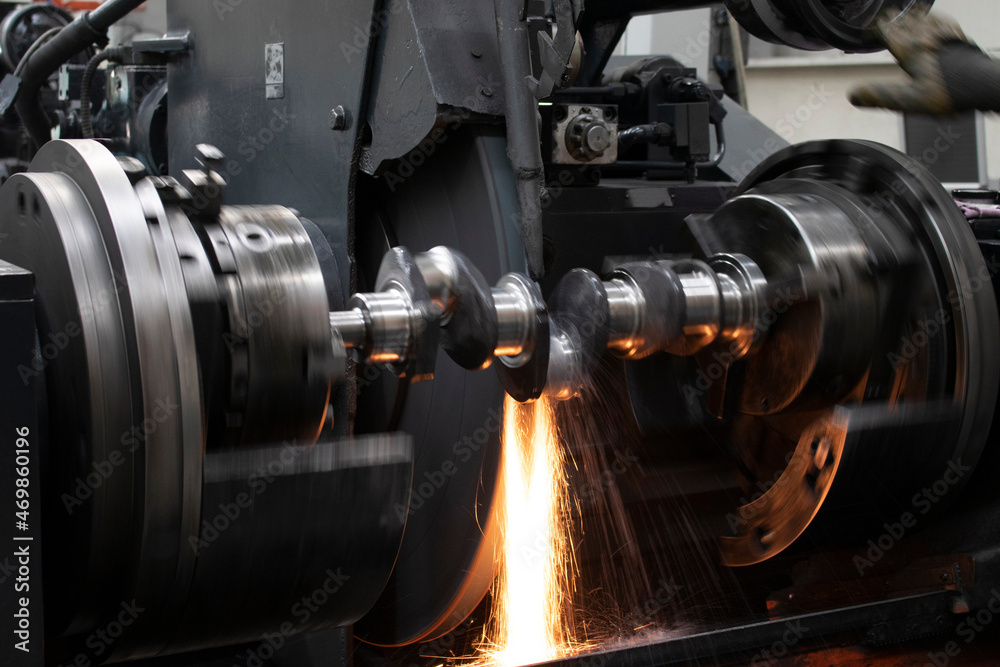
クランクシャフトの切削工程について、興味を持っている方は多いのではないでしょうか。しかし、「切削プロセスはどうなっているのか?」「どのように始めれば良いのか?」と悩んでいる方もいるかもしれません。そんな疑問を持つあなたのために、この「クランクシャフトの切削工程完全ガイド」を作成しました。
この記事は、以下のような方々に向けています。
- クランクシャフトの切削工程を理解したい。
- 効率的に切削を行い、高品質な製品を作りたい。
- 切削に必要な基本知識や技術を習得したい。
クランクシャフトは、自動車や機械の心臓部ともいえる重要なパーツです。その切削工程を理解することで、製造現場での工程改善やコスト削減に繋がります。本記事では、クランクシャフトの切削の基本から、実際の工程、さらに成果を最大化するためのテクニックまでを詳しく解説します。切削に対するあなたの理解を深め、成功へと導く一助となれば幸いです。
1. クランクシャフトの切削とは
1-1. クランクシャフトの定義と役割
クランクシャフトは、エンジン内部でピストンの往復運動を回転運動に変換する重要な部品です。以下の役割を果たします。
- エネルギー変換:燃焼による直線運動を回転運動へ変換し、動力を伝達する。
- トルクの調整:フライホイールと連携し、エンジンの回転をスムーズにする。
- エンジン出力の安定化:バランスウェイトにより振動を軽減し、エンジンの効率を向上させる。
1-2. クランクシャフトの基本構造
クランクシャフトは、いくつかの重要な部分で構成されています。
部位 | 役割 |
---|---|
メインジャーナル | クランクシャフトをエンジンブロックに固定し、回転運動の軸となる。 |
クランクピン | コンロッドと接続し、ピストンの往復運動を回転運動に変換する。 |
カウンターウェイト | 回転バランスをとり、振動を抑制する。 |
オイル通路 | 内部にオイルを通し、摩耗を防ぐための潤滑を行う。 |
クランクシャフトは高精度な切削加工が求められ、特にジャーナルやピンの円筒度や表面仕上げがエンジンの性能に大きく影響します。
2. クランクシャフトの切削加工の重要性
2-2. 切削加工の目的
クランクシャフトの切削加工は、エンジンの性能や耐久性を左右する重要な工程です。以下の目的があります。
- 高精度な形状維持:クランクシャフトの回転バランスを保ち、エンジンの振動を抑える。
- 滑らかな表面仕上げ:摩擦と摩耗を低減し、エンジン寿命を延ばす。
- 適切な寸法公差の確保:コンロッドやベアリングと適合し、スムーズな動作を実現する。
2-3. クランクシャフトの切削における課題
クランクシャフトの切削加工には、いくつかの技術的課題が存在します。
課題 | 内容 |
---|---|
高精度の要求 | クランクピンやメインジャーナルの円筒度・真円度をμm単位で管理する必要がある。 |
切削負荷の大きさ | 材料が高強度なため、工具摩耗が早く、切削条件の最適化が求められる。 |
バランス調整 | クランクウェブの重量バランスを取り、回転時の振動を最小限にする必要がある。 |
加工熱と変形 | 切削時の発熱により、寸法変化や残留応力が発生しやすい。 |
高効率加工の必要性 | 大量生産の場合、加工時間短縮とコスト削減が求められる。 |
これらの課題を克服するために、高精度なCNC加工機や特殊工具、研削加工を組み合わせた工程が採用されます。
3. クランクシャフトの切削加工の工程
3-1. 材料の選定
クランクシャフトの性能を最大限に引き出すためには、適切な材料の選定が重要です。一般的に使用される材料には、炭素鋼、合金鋼、鋳鉄などがあります。炭素鋼は加工しやすく、コストも抑えられるため広く使用されますが、高負荷の環境では合金鋼が選ばれます。鋳鉄は振動吸収性に優れており、大型のエンジンに採用されることが多いです。
材料選定時には、以下の点を考慮します。
- 強度と耐摩耗性
- 加工性とコスト
- 使用環境と負荷条件
3-2. 切削条件の設定
クランクシャフトの切削では、加工精度を確保しつつ、工具寿命を延ばすために適切な切削条件を設定する必要があります。主な要素として、以下の点が挙げられます。
- 切削速度:過度な速度設定は工具の摩耗を早めるため、適切なバランスが必要
- 送り速度:仕上げ面の粗さを考慮しながら適正な値を設定
- 切込み深さ:工具寿命と加工効率を両立する範囲で設定
- クーラント:加工熱の抑制と工具の冷却に適切な種類を使用
- 工具選定:高硬度材には超硬工具やCBN工具を使用
適切な切削条件を設定することで、加工の安定性が向上し、高精度な仕上がりを実現できます。
3-3. 加工後の検査と品質管理
加工が完了したクランクシャフトは、厳格な検査と品質管理を行うことで、長期間にわたり安定した性能を発揮できます。主な検査項目は以下の通りです。
- 寸法精度:三次元測定機を用いて厳密にチェック
- 表面粗さ:触針式粗さ計で仕上げの状態を確認
- 硬度試験:ブリネル硬度計やロックウェル硬度計を使用
- ひずみ検査:光学測定やレーザー計測によるチェック
- バランス調整:動釣合い試験機で動的バランスを調整
これらの検査を徹底することで、品質のばらつきを防ぎ、耐久性の高いクランクシャフトを提供することが可能になります。
4. クランクシャフトの用途
4-1. 自動車産業におけるクランクシャフト
自動車エンジンの心臓部とも言えるクランクシャフトは、ピストンの往復運動を回転運動に変換する重要な役割を果たします。特に、自動車産業では以下のような特徴が求められます。
- 高強度・高耐久性:エンジン内部の過酷な環境に耐えるため、高強度な合金鋼や鍛造鋼が使用される。
- 軽量化技術:燃費向上のため、強度を維持しつつ軽量化が進められている。
- 高精度加工:振動や騒音を最小限に抑えるため、高精度な切削加工とバランス調整が施される。
また、電動車の普及により、クランクシャフトの需要は一部減少傾向にあるものの、ハイブリッド車では依然として重要な部品であり続けています。
4-2. 航空機や産業機械での利用
クランクシャフトは、自動車以外の分野でも幅広く活用されています。
航空機
航空機のエンジンには、高精度かつ軽量なクランクシャフトが必要です。特に、小型航空機やレシプロエンジンを搭載したヘリコプターでは、耐熱性や耐久性に優れたクランクシャフトが使用されています。
- 高精度設計:航空機エンジンでは、極めて精密な加工が求められる。
- 耐熱合金の使用:高温環境に耐えうるニッケル合金やチタン合金が採用される。
- 軽量化技術の適用:カーボンコンポジットや特殊合金を用いることで、重量を最小限に抑える。
産業機械
クランクシャフトは、さまざまな産業機械や発電設備にも使用されています。特に、大型のディーゼルエンジンやコンプレッサーなどに不可欠な部品です。
- 発電設備:ディーゼル発電機のエンジンに使用され、長時間の連続運転に耐える耐久性が求められる。
- 油圧機械・コンプレッサー:ピストンを駆動する装置において、回転運動を生み出す重要な構成要素となる。
- 建設機械:ブルドーザーやショベルカーのエンジン部品として採用され、過酷な環境下でも耐えられる強度と耐摩耗性が必要。
このように、クランクシャフトは自動車だけでなく、航空機や産業機械といったさまざまな分野で欠かせない部品として活躍しています。
5. クランクシャフト加工機の選定
5-1. 加工機の種類と特徴
クランクシャフトの加工には、さまざまな専用機械が使用されます。それぞれの加工機には異なる特徴があり、用途や精度の要求に応じて選定されます。
- CNC旋盤
- 高精度な切削加工が可能で、クランクピンやジャーナル部分の形状加工に適している。
- プログラム制御による自動化が可能で、大量生産に向いている。
- クランクシャフト研削盤
- 高精度な仕上げ加工が可能で、振動を抑えた加工ができる。
- ジャーナルやピン部の表面仕上げに特化している。
- フライス盤
- クランクシャフトの端部加工やキー溝加工に使用される。
- 切削工具を取り替えることで、多用途に対応可能。
- ホーニングマシン
- 微細な表面仕上げを行い、摩擦低減や耐久性向上に貢献する。
- シリンダーやベアリングとの適合性を高めるために重要な工程となる。
5-2. 使用方法と注意点
クランクシャフト加工機を使用する際には、以下の点に注意する必要があります。
- 適切な切削条件の設定
- クランクシャフトの材質に応じた最適な切削速度や送り量を選定することが重要。
- 過剰な切削負荷をかけると、加工精度の低下や工具の寿命短縮につながる。
- 加工機の剛性と精度の確認
- 高精度な加工を行うためには、振動を最小限に抑えた剛性の高い機械を選定することが求められる。
- 定期的な機械の点検やメンテナンスが必要。
- 工具の管理と交換
- クランクシャフト加工では、切削工具の摩耗が精度に影響を与えるため、適切なタイミングで交換することが重要。
- 研削盤を使用する場合、砥石のドレッシング(再成形)を適切に行う必要がある。
- 安全対策の徹底
- 高速回転する加工機を扱うため、作業者の安全管理が不可欠。
- 保護具の着用や、機械のインターロック機能を活用する。
クランクシャフト加工機の選定には、加工精度・生産性・コストのバランスを考慮し、それぞれの特徴を理解した上で適切な機械を選ぶことが重要です。
まとめ
クランクシャフトの切削工程は、精密な加工が求められる重要なプロセスです。この記事では、材料選定、工具の種類、切削条件、仕上げ方法など、各工程のポイントを詳述。効率的な生産と高品質な仕上がりを実現するためのベストプラクティスを紹介し、技術者の理解を深める内容となっています。